Breadcrumb
Progressive dies expedite the processing operations
During the quotation phase, Minifaber's technicians design and manufacture the die most suitable for producing the finished product without wasting resources. The pros and cons of progressive dies are listed below, along with their recommended applications.
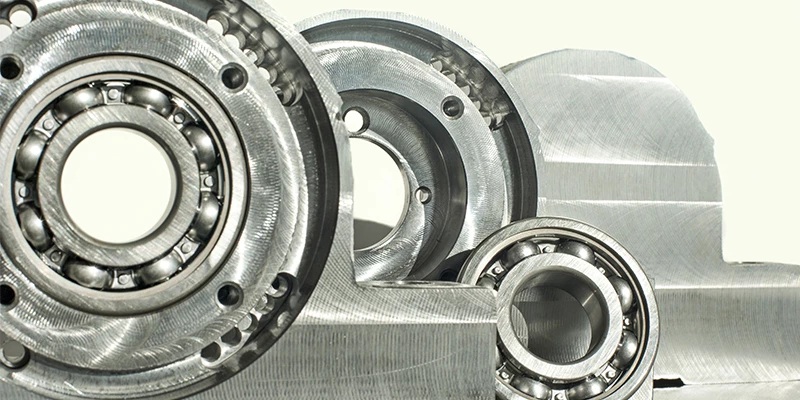
Progressive dies: stations and fixed steps
A progressive die’s functionality is based on a series of pressing stations arranged at a fixed distance from one another, which, in technical terms, is called a “step”. Each pressing station is capable of performing one processing operation upon the sheet metal, which, by moving on to the next step with each stroke of the press, is ultimately subjected to all the various steps until the finished part is obtained.
The number of pressing stations depends on the complexity of the product to be obtained, its size, and of the number of parts that are produced with each stroke.
The pros and cons of a progressive die
The first advantage offered by a progressive die is that, with each stroke of the press, the various pressing stations work on different levels simultaneously and allow for various processing operations to be carried out. In this manner, it is possible to produce extremely complex parts, and to obtain one or more finished parts with each stroke, thus reducing the work times with respect to those required by transfer dies.
The disadvantage of a progressive die, however, is that the part remains attached to the base material throughout each step, and is only separated by shearing during the final processing phase.
Recommended applications for progressive dies
Progressive dies are particularly suitable for the production of small components in large numbers. This is due to the need to amortize the cost of manufacturing the die itself, which can be rather high because, in addition to the complexity of the die itself, it is also necessary to provide a sheet guide, a lifter, and all the components necessary for transporting the material through the various stations. In the case of small components in large batches, however, progressive dies are excellent solutions for obtaining high-quality pressed parts with reduced time frames with respect to those offered by transfer dies.