Breadcrumb
Steel processing: guaranteed quality, precision and performance
All the advantages of stainless steel processing with Minifaber
Steel processing, and stainless steel processing in particular, is one of the most sought-after specializations in high-precision industrial sectors. Due to its structural characteristics – high resistance, durability, and hygiene – stainless steel is widely used in the medical, food, electromechanical, household appliance, automotive, energy distribution, and nautical sectors.
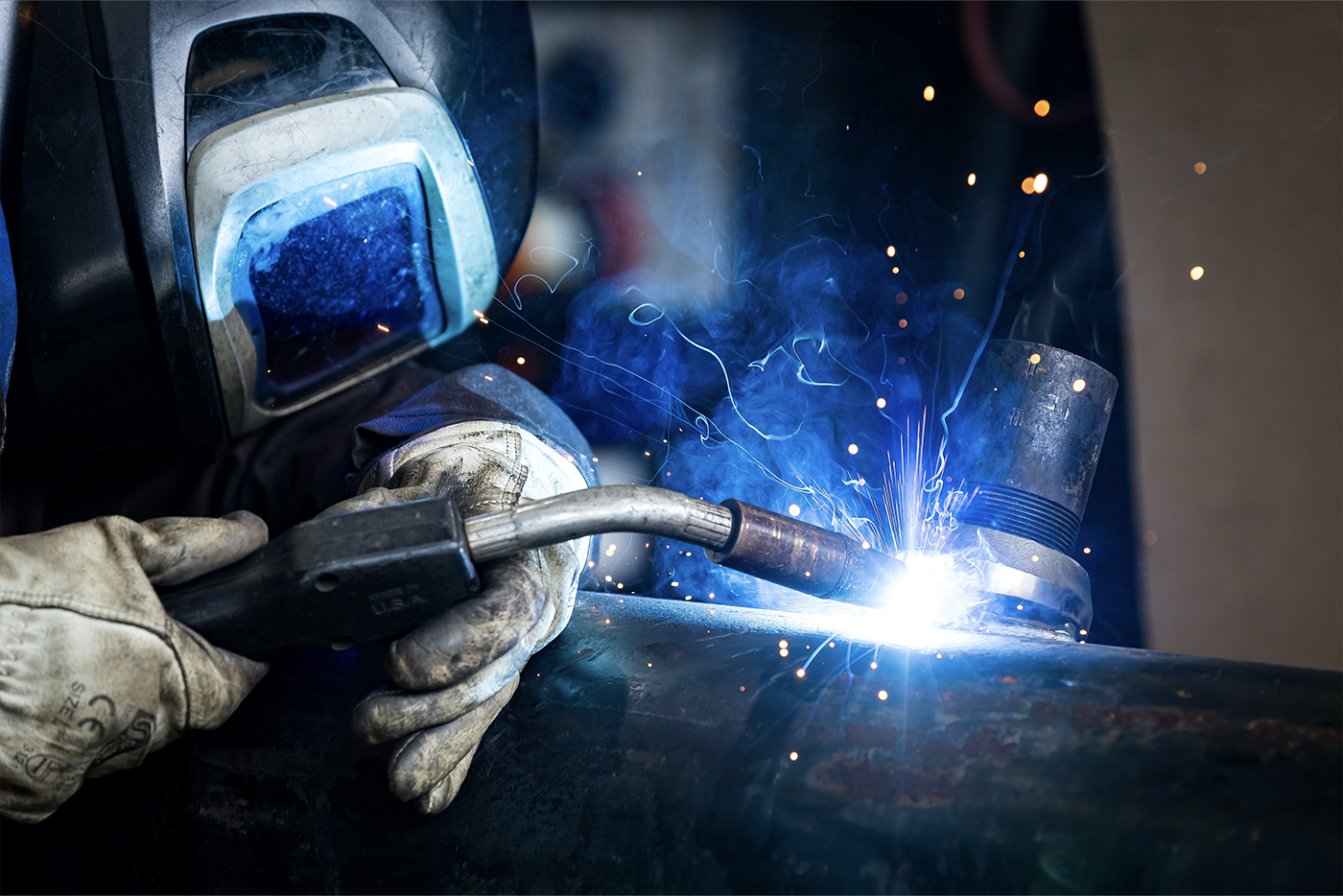
Steel processing, and stainless steel processing in particular, is one of the most sought-after specializations in high-precision industrial sectors. Due to its structural characteristics – high resistance, durability, and hygiene – stainless steel is widely used in the medical, food, electromechanical, household appliance, automotive, energy distribution, and nautical sectors.
In this article, we will look at the main operations involved in stainless steel processing, its applications, and the technical advantages it offers.
How stainless steel processing works
Stainless steel processing is a complex process that transforms sheet metal or semi-finished products into high-precision technical components ready for integration into industrial, medical, or food applications.
Each phase requires specific skills and appropriate technologies to ensure compliance with dimensional tolerances and the physical properties of the material.
Cutting and shaping
The process begins with flat cutting and shaping, which can be done by punching or laser cutting. These methods enable the creation of complex and precise geometries, even on thin sections, with reduced margins of error and minimal material deformation.
Bending
This is followed by bending, which allows the shape of the metal to be modified without compromising the material's integrity. This is particularly important for the production of box sections, bent parts generally used to make components or parts of welded assemblies, casings, or structural elements where maximum reliability is required.
All these processes are carried out using CNC machines and automated or robotic systems, which ensure consistent quality, high repeatability, and optimized production times, even for large-scale orders.
Deep-drawing
The deep drawing technique is used to produce hollow three-dimensional pieces such as pots, sinks, sterilization chambers, and kitchen robots. The most complex shapes can be created by deforming the material in a controlled manner.
Stainless steel welding
A fundamental step is the welding of stainless steel, which is carried out using MIG, TIG, and LASER technology, depending on the item's thickness and the required functional characteristics. All these processes, when properly developed, enable the production of joints with good and consistent mechanical characteristics, free from defects, and with an aesthetic finish that meets industry standards.
Surface treatments
Finally, components can undergo surface treatments that enhance their appearance, improve corrosion resistance, or increase compatibility with specific environments. Electropolishing, for example, is widely used in the medical sector, while satin finishes are common in the food and household appliance industries. Passivation, on the other hand, improves resistance to oxidation.
Why choose stainless steel?
Stainless steel is a metal alloy that offers a unique combination of properties:
Corrosion resistance, thanks to its chromium content (minimum 10.5% but generally over 17%), which forms a passivating layer on the surface;
Excellent workability in its austenitic and ferritic variants, even when cold deformed;
High mechanical resistance, suitable for structural applications or in environments subject to mechanical stress;
Hygiene and cleanliness, essential in healthcare and food applications;
Aesthetics, for design applications and visible finishes.
Thanks to these characteristics, stainless steel is suitable for complex processes where oxidation resistance, precision, and high performance are required.
Stainless steel processing: the advantages of professional welding
Welding is one of the most complex stages in stainless steel processing, as it requires advanced skills and high-precision equipment to ensure strong, durable joints. Depending on the specific requirements of the project and the type of material to be treated, Minifaber uses different welding technologies, each with its own distinctive advantages.
TIG steel welding
TIG welding is an ideal choice for joints that require high precision and good penetration of the welded joint. This process is particularly suitable for working on thin materials, as it allows the heat input to be concentrated in a targeted and controlled manner, minimizing deformation of the sheet metal. Due to its ability to create uniform and strong joints, TIG welding is widely used in applications where reliability and aesthetic finish are essential, such as in the medical and food industries, as well as other high-quality applications.
MIG steel welding
MIG welding, on the other hand, is ideal for working on thicker materials and higher productivity requirements. This process allows for faster operation, optimizing time and costs. Although the aesthetic quality of the joint may be less perfect than with TIG welding, MIG welding is ideal for industrial applications where speed and thickness are more important.
Robotic welding
Robotic welding is an advanced solution for mass production or applications requiring maximum repeatability. Industrial robots make it possible to optimize welding times while ensuring consistent quality and exact parameter control. Robotic welding operations are particularly advantageous for mass-producing standardized components, as they offer high levels of safety and minimize human error.
Laser welding
Laser welding achieves even greater precision, combined with excellent welding penetration, high speed of execution, and, thanks to minimal heat input, limited sheet metal deformation.
Strict controls
In all cases, Minifaber guarantees rigorous quality control on every welded joint. This includes visual inspections, non-destructive testing such as penetrating liquids, radiography, or ultrasonics. If required, in-depth metallographic testing is conducted to confirm the strength and reliability of the joint, ensuring that every product meets the quality standards required by customers.
Minifaber's expertise in steel processing
Since 1960, Minifaber has been a benchmark for cold steel processing.
Minifaber's integrated approach allows it to manage all phases: design, prototyping, sampling, and mass production. Depending on requirements, internal departments work together to offer a complete, assembled, and tested finished product.
Each stainless steel processing operation is customized based on:
type and thickness of sheet metal
final function of the component
required quantities and tolerance margins
finishing requirements and protective treatments
Thanks to CNC machinery, hydraulic presses, and state-of-the-art welding systems, Minifaber guarantees a reliable, scalable, and competitive service.
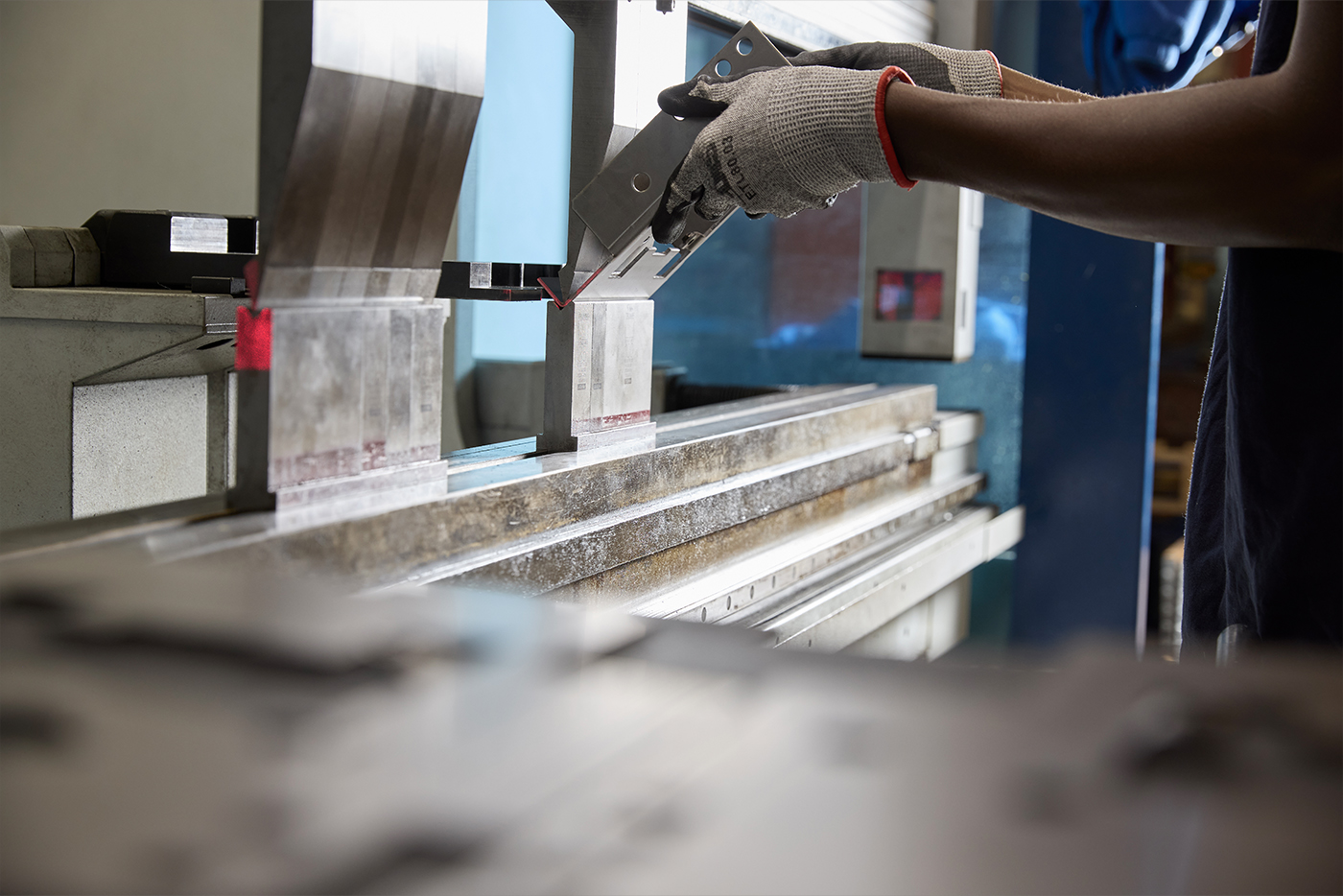