Breadcrumb
TIG welding aluminum: a precision technique for strong, clean joints
An ideal technology for superior joints
TIG welding aluminum is one of the most reliable solutions for obtaining strong, neat joints with no structural defects. It is used for thin but also thicker sections and components with high functional value.
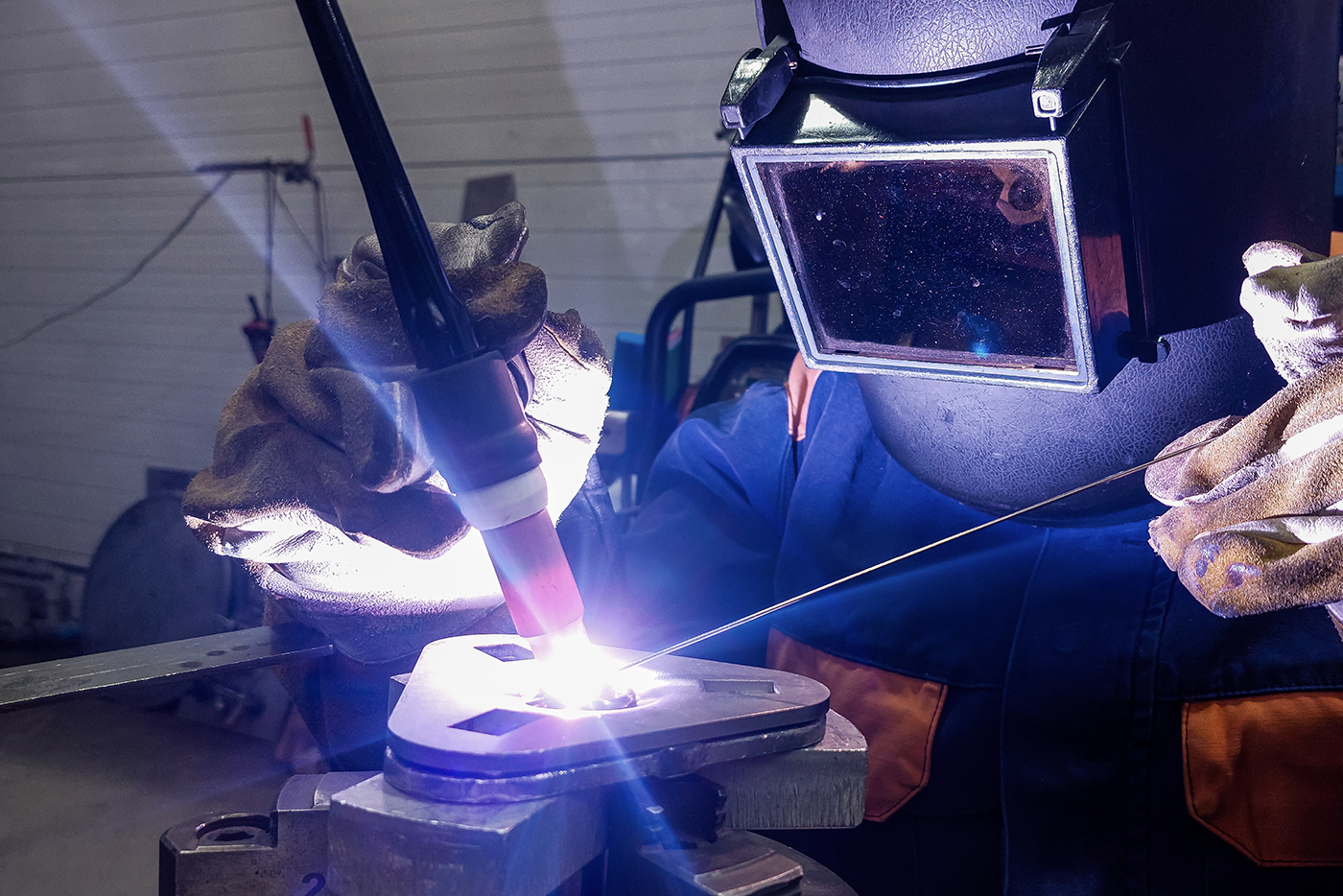
TIG welding aluminum is one of the most reliable solutions for obtaining strong, neat joints with no structural defects. It is used for thin but also thicker sections and components with high functional value.
Minifaber uses this technique for the professional machining of aluminum and its alloys, ensuring excellent results in terms of penetration, joint precision, and finish. All this is thanks to the experience of our operators, the monitoring of parameters, and the use of cutting-edge machinery.
How TIG welding works
TIG (Tungsten Inert Gas) welding, also known as GTAW (Gas Tungsten Arc Welding), is an arc welding process that uses a non-consumable tungsten electrode to generate the electric arc between the electrode and the workpiece.
The electric arc is transferred from the electrode to the workpiece by an inert gas that is ionized when the electric current passes through it. Argon is generally used because it protects the molten pool from atmospheric contamination, thereby preventing oxidation and inclusions. It is sometimes mixed with helium to optimize welding speed and penetration.
The process can be carried out with or without filler material, depending on the joint's geometry and the thickness of the parts. The electrode does not melt during the process: only the base metal (and any filler wire or rod) melts due to the concentrated heating action. This allows exact control of the welding pool, making the process ideal for components that require clean, thin joints with high mechanical integrity.
In addition, AC (alternating current) generators are used for welding aluminum, as they are able to break the alumina layer, ensuring a cleaner, crack-free weld.
Preparing aluminum before welding
Proper preparation of the workpiece is essential for the quality and strength of the welded joint. Aluminum has a naturally occurring surface layer of oxide (alumina) that melts at approximately 2,050°C, a temperature significantly higher than the melting point of the base metal (approximately 650°C). If not removed, the oxide can compromise arc penetration and cause inclusions, porosity, and cracks in the welded area.
For this reason, before TIG welding, it is essential to remove the oxidized layer using mechanical methods—for example, by brushing with dedicated stainless steel brushes, light grinding, or a preheating treatment.
The use of alternating current in aluminum welding allows the alumina layer to be broken during the positive half-wave and the weld to penetrate during the negative half-wave.
Contaminants such as grease, oil, dirt, and grinding residues must also be avoided in the vicinity of the edges to be welded: the piece must be degreased with suitable solvents (such as acetone or specific products for aluminum), and consumables such as gas and filler wire must not be damp. All preparation work must be carried out immediately prior to welding, to avoid further alterations to the metal.
To avoid defects, Minifaber applies a careful preparation protocol:
mechanical or chemical cleaning of the surface;
use of AC/DC generators, useful for breaking oxide during welding;
selection of compatible filler materials, improving the weldability of the joint, and preventing dangerous defects in the welded joint, such as cracks and porosity
The advantages of TIG welding Aluminum
Aluminum is a material that requires in-depth technical knowledge to be welded correctly. It has a relatively low melting point (around 660°C), but is also an excellent thermal conductor: this results in rapid heat dispersion, which can affect the quality of the weld if not handled with the necessary expertise.
Not all aluminum alloys are weldable. Before starting any welding work, it is essential to ensure that the chosen alloy is weldable
TIG welding is particularly effective for aluminum thanks to a series of advantages that make it suitable for both precision work and work requiring high aesthetic and mechanical quality:
Precise control of heat input
The TIG process is characterized by a well-concentrated welding arc, which minimizes material deformation, particularly critical when working with thin gauges or delicate geometries.
Clean and uniform joints
Thanks to the absence of spatter and slag, TIG welding produces smooth, visually homogeneous welds with no surface imperfections, often without the need for mechanical or aesthetic post-processing.
Flexibility in the use of filler material
When conditions allow (for example, with joints in perfect contact), welding can be performed without adding material, but in the case of aluminum, the correct use of filler metal improves weldability.
High joint strength and stability
When performed correctly, TIG welding ensures optimal metallurgical continuity between the edges, with deep penetration and no inclusions, resulting in mechanical performance that is comparable or superior to that of the base material.
Process parameters and quality control
Every TIG weld requires the correct configuration of fundamental variables, including:
type of current (alternating for aluminum, with integrated cleaning function);
diameter of tungsten electrode with specific tip geometry for welding aluminum with alternating current
inert gas flow rate, which protects the melting pool from atmospheric contamination;
distance between the electrode and the workpiece, which must remain constant to ensure arc stability.
In the Minifaber departments, the process is constantly monitored by qualified operators and control systems that check the quality of the bead, penetration, and the presence of any surface or internal defects, including through non-destructive tests and macrographs performed on preliminary welding roots for process fine-tuning.
When to choose TIG welding aluminum
TIG welding is particularly suitable for:
parts with complex geometries or precision joints;
thin gauges (even less than 1 mm);
uses where high aesthetic and functional standards are required, such as in the medical, electronic, or food industries.
For greater thicknesses or processes requiring high productivity, MIG welding can be considered as an alternative, which Minifaber offers as a complementary service.
Trust Minifaber for TIG welding aluminum
Since 1960, Minifaber has been a leader in cold metal working, thanks to an approach that combines technical expertise, advanced technologies, and quality craftsmanship.
TIG welding aluminum is one of the key processes within our services, performed both manually and with automated or robotic systems, depending on the project.
Contact us for advice or to request a quote: our team will guide you in choosing the most suitable welding technique for your aluminum components.