Breadcrumb
Laser cutting iron: What it is, how it works, and why it is worth it
Laser cutting iron: the ideal technology for precise and fast machining
Laser cutting iron allows for customised workmanship, high-quality finishes and shorter production times. Thanks to the use of cutting-edge machinery and technical expertise, Minifaber is able to manufacture semi-finished and finished iron products to meet any design requirement.
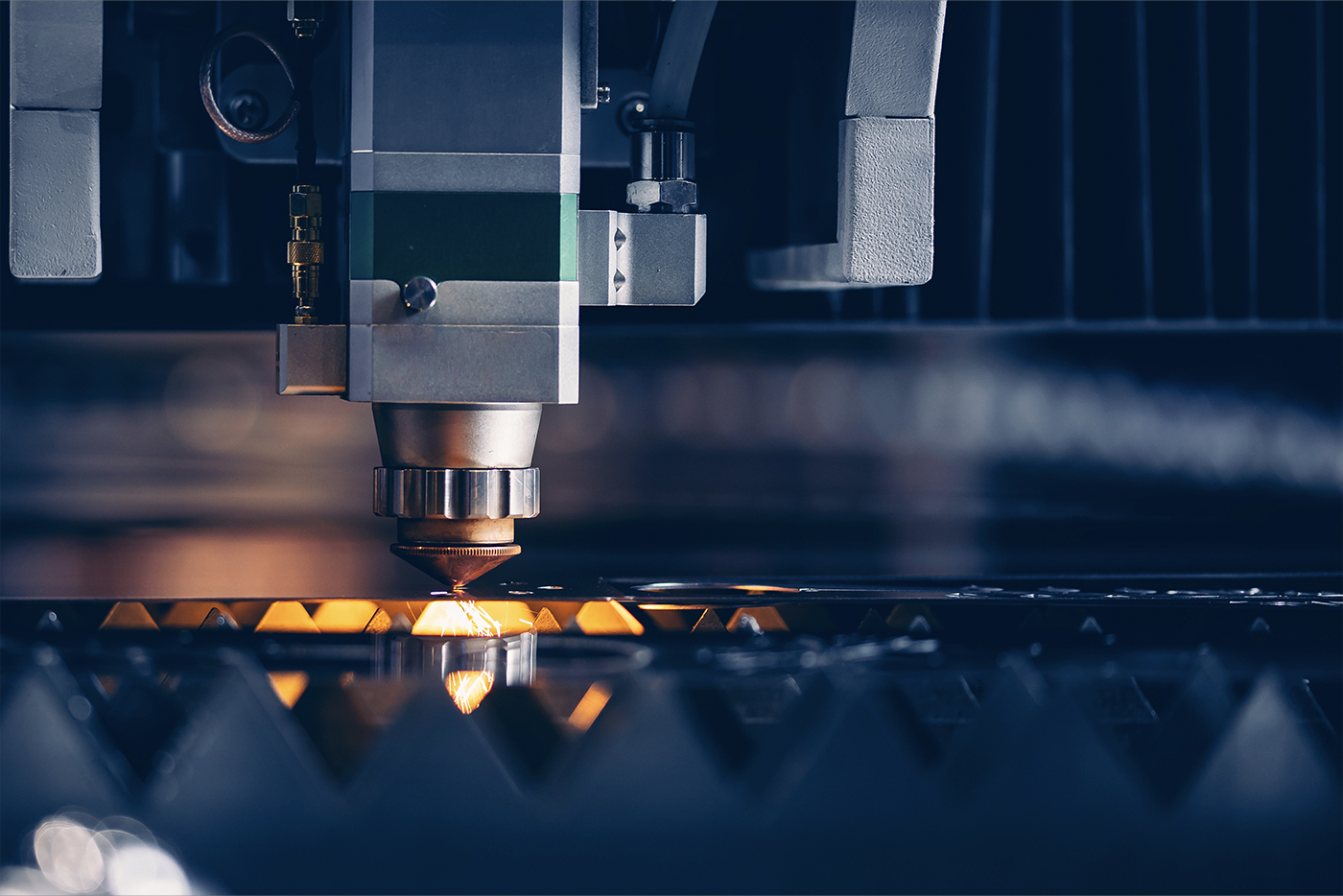
Laser cutting iron allows for customised workmanship, high-quality finishes and shorter production times. Thanks to the use of cutting-edge machinery and technical expertise, Minifaber is able to manufacture semi-finished and finished iron products to meet any design requirement.
In this guide you will learn:
how laser cutting iron works
what are the main advantages?
Minifaber's customized service
How laser cutting iron works
Laser cutting is a high-precision thermal process that uses a coherent, concentrated, and modulated beam of light to melt, vaporize, and therefore cut metal. In the specific case of iron, the laser beam—generated by CO₂ or solid sources—is focused on a point with a very small diameter, generating very high temperatures of around 3,000 °C. The energy thus concentrated allows cutting, drilling, and shaping to be carried out with high geometric accuracy, even on materials of considerable thickness.
Minifaber uses state-of-the-art CNC systems designed for reliable machining on both small series and large batches. Integrated automation and computerized numerical control allow precise management of the cutting path, feed speed, laser power, and assist gas parameters, which can be adjusted according to the material and thickness.
The process consists of the following stages:
Technical definition of the project
We often work with customers to define the design of the product to be laser cut. Once the design of the piece to be produced has been defined and approved, it is used by Minifaber's CAM software, which utilises a nesting program to determine the optimal layout (in terms of space and orientation) of the pieces to be cut from a flat sheet of standard-sized sheet metal.
The nesting program is imported onto the cutting machine where the interface with the CNC system allows all cutting parameters to be set in detail: feed speed, laser power, type of assist gas, beam focus, as well as creating the cutting path.
The iron sheets are taken from an automated warehouse and placed on the laser cutting machines. All these operations are fully automated. The operating parameters are retrieved directly from the CNC database, minimizing manual tasks.
Automated laser cutting
Depending on production requirements, Minifaber uses:
Punch-laser combination machines; ideal for cutting, but not only: they can also be used for small stamping, bending, and threading operations. Furthermore, these machines combine laser with punching technology.
2D and 3D laser systems, equipped with CO₂ sources (suitable for high-quality cuts on flat sheets) or fiber (more suitable for high speeds on highly reflective materials such as copper and for 3D processing);
Technical gas assistance systems: The use of oxygen allows localized combustion to increase cutting speed on thicker materials, and only for iron, while nitrogen is used for all other materials, including iron, for cleaner cuts free of oxidation, particularly suitable for aesthetic purposes or for subsequent surface treatments or welding.
Post-processing cycle management
Once cutting is done, the parts are moved on to the next steps (bending, welding, assembly) and always checked for size and quality using optical and digital measuring tools.
The entire process is traceable and optimized in line with Industry 4.0 standards, with real-time performance monitoring and direct interfacing with the company's ERP and MES systems.
The advantages of laser cutting iron
Laser cutting iron is a cutting-edge technology in sheet metal working, particularly suitable for components intended for highly specialized industrial sectors such as mechanical, electrical, electromechanical, automation, and functional design. It is a solution that combines quality performance, time optimization, and indirect cost reduction, with real benefits throughout the entire production chain.
Superior cutting quality
The cutting process takes place by localized melting, using a high-energy laser beam that does not exert any mechanical stress on the material. This eliminates the risk of thermal or structural deformation, ensuring clean, burr-free edges with reduced surface roughness. In most cases, the resulting finish does not require deburring or finishing operations, resulting in significant savings in time and resources.
Consistent precision on complex geometries
Thanks to the small diameter of the laser beam and CNC, we can perform cuts with extremely high precision, even on complex profiles or with strict dimensional tolerances. The process is ideal for creating complex shapes, maintaining repeatability and consistency even on large production runs. Punch-laser combination machines, therefore, enable the creation of complex laser-cut shapes and high-precision holes through punching. Minifaber uses CAD/CAM software for direct machining programming, optimizing cycle times and minimizing human error.
Operating speed and cycle time reduction
Laser cutting is one of the fastest and most flexible methods for processing iron. The possibility of using technical gases, such as oxygen (for faster cuts on thick sheets) or nitrogen (to prevent oxidation at edges), allows for modulating the process according to specific applications. Integrated automation, with loading/unloading systems and optimized nesting, further contributes to the efficiency of the entire production cycle.
Adaptability to all production requirements
Laser cutting can be used both in the prototyping phase and in mass production, even on variable batches. It is compatible with various sheet metal formats and thicknesses (up to 6 mm for iron). It can be seamlessly integrated with subsequent processing stages such as bending, welding, threading, or surface treatments. Operational flexibility makes it an ideal tool even in just-in-time contexts or with high product code variability.
Sustainability and optimization of materials
The laser process is also highly efficient from an environmental point of view. The absence of lubricants or additives, reduced waste production, and the possibility of optimizing the cutting layout using nesting software, all contribute to reducing environmental impact and raw material waste. Moreover, energy consumption can be modulated according to the power output and the gas used, making the entire process more sustainable than other mechanical technologies.
Minifaber's laser cutting iron service
Minifaber provides a highly specialized laser cutting iron service, suitable for both prototyping and mass production. Our production capacity encompasses orders with varying levels of complexity, ensuring maximum adaptability in terms of volume, geometry, and thickness.
Our service includes:
● processing of iron sheets of various thicknesses and formats
● production of semi-finished parts and finished components ready for assembly
● customized programming via CNC systems to ensure repeatability and precision
● integration of laser cutting with bending, threading, punching, and assembly, if required
The use of high-efficiency equipment—including punch-laser combination machines—and the availability of technical gases selected according to the material and the desired result (oxygen or nitrogen) allow Minifaber to offer consistent quality output with optimized cycle times. An in-house technical team supports the customer in defining the process, from design to delivery.
Request a personalized technical consultation
If you need to integrate laser cutting iron into your production process, Minifaber provides a technical team for feasibility analysis, design support, and cost estimates. Contact us for expert advice or a detailed quote, with no obligation. We offer tailor-made solutions and high-precision machining, optimized for industrial requirements.
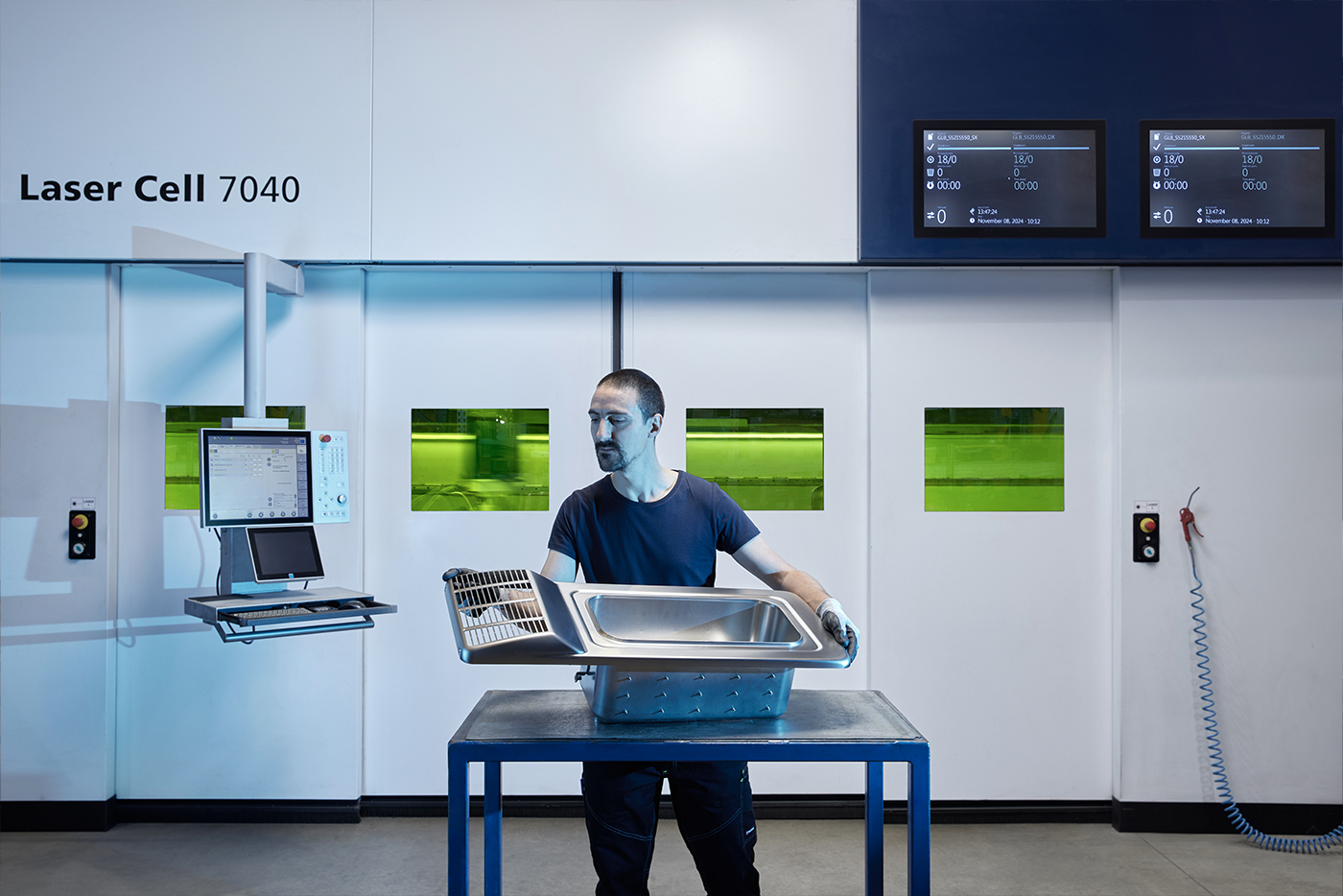