Breadcrumb
MIG welding aluminum: do you know the advantages of Minifaber?
MIG welding aluminum can become a real challenge if the appropriate machinery is not used and the process is not carried out with care. At Minifaber we specialize in metal cold working and this article will explain how this welding process takes place, what are its advantages and what services we offer customers.
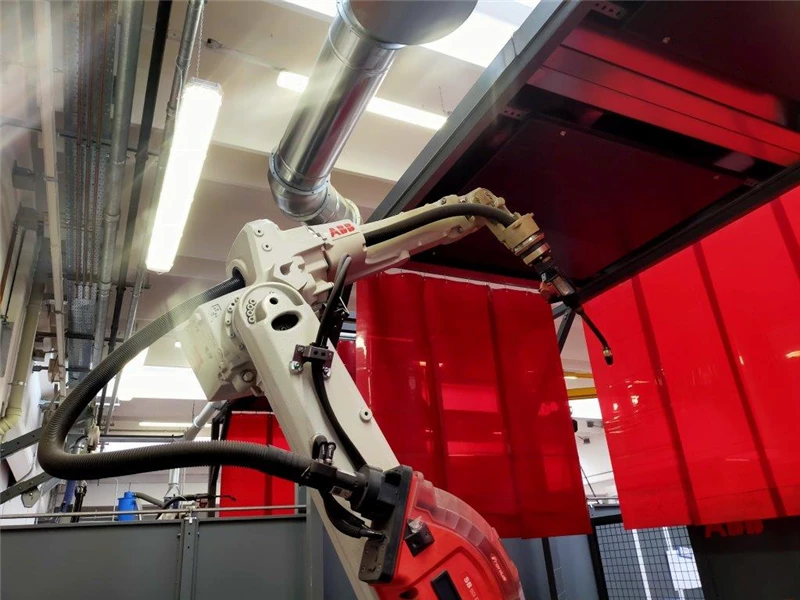
Let's take a closer look at how the MIG welding aluminum takes place:
- what MIG welding is and how it happens
- the advantages
- Precautions before starting
- Minifaber services
How does MIG welding aluminum work?
MIG - Metal Arc Inert Gas - welding aluminum, also commonly called "wire welding", is an electric arc welding process, where the filler material shaped like a wire is melted drop by drop in the welding joint.
Robotic welding
Aluminum welding is now increasingly automated, thanks to the use of anthropomorphic robots that guide the torch on the welding joint of the piece to be welded.
Robot, wire feed, welding parameters such as current, voltage, frequency, are managed in synergy to obtain the best performance of the welded piece.
The use of technological machinery for MIG welding benefits the entire process in terms of:
- precision of the final result, because each parameter is automatically maintained and controlled by the machine for the entire duration of the welding once set by the operator
- time optimization, because the operator can perform other jobs such as preparing a new piece to be welded, checking the weld and more during robotic welding.
- resource optimization, because the robot saves the operator from long continuous and repetitive welding hours that cause physical fatigue as well as discontinuity and variability of the welds.
The advantages of MIG welding aluminum
MIG welding aluminum offers multiple advantages such as:
- filling uneven edges
- welding large thicknesses
- high welding speed
- possibility of improving the welded joint seals thanks to the contribution of the correct and most suitable filler material
The intrinsic qualities of aluminum also contribute to this:
- it is a very ductile and light metal
- it resists corrosion
- it has excellent thermal and electrical conductivity
- it has a fairly low melting temperature - around 1220° F
Precautions for welding aluminum
Despite its advantageous intrinsic characteristics, some difficulties may be found welding aluminum. First, aluminum is coated with a very hard natural oxide called alumina, with a higher melting point than aluminum and with a density higher than that of the base metal.
For this reason, it is necessary to avoid that the alumina ends up inside the molten aluminum bath because it would generate brittle joints and cracks.
Before welding, the alumina layer must be mechanically removed or the filler material must be accurately selected.
Secondly, aluminum is very often used in an alloy with other elements to obtain materials that are more mechanically and corrosion resistant.
Also in this case the alloy to be welded must be taken into account by making the appropriate choices of welding parameters and filler materials.
MIG welding aluminum with Minifaber
Thanks to our technologically advanced machinery, to our constant investment in development and research, to the welding controls and to the choice of the appropriate filler materials, Minifaber can guarantee excellent MIG welding service aluminum service:
- accurate
- safe
- convenient
Our staff, in fact, perfectly manages the internal machine park, offering customers MIG welding applicable to both small batches and large quantities, even for staggered productions over time.