Breadcrumb
Metal moulding and customer service: 2 complex, finished and assembled products for the kitchen robotics sector
Metal moulding and customer service: 2 complex, finished and assembled products for the kitchen robotics sector.
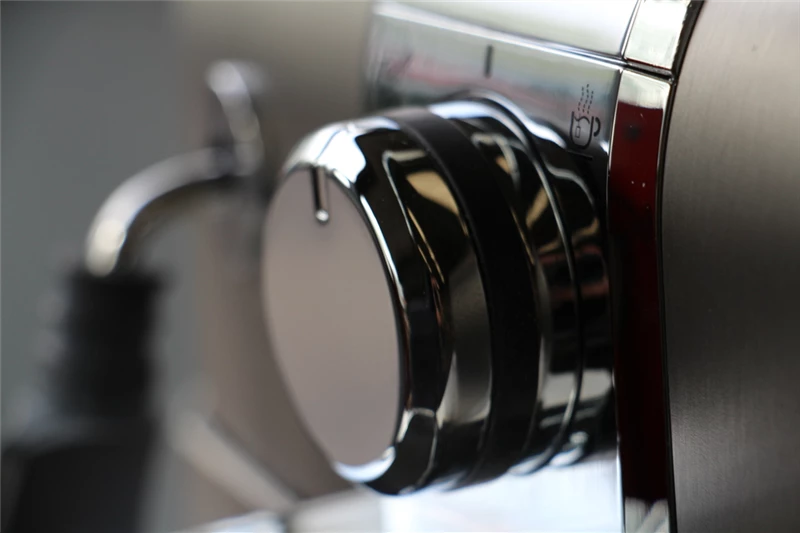
Minifaber is a company which, in addition to providing classic cold sheet processing and metal moulding processes (metal shearing, deep drawing sheet metal, bending, punching, laser cutting, welding, etc.), can also design and construct complete, finished and assembled products.
The staff’s advanced level of technical training, the constantly updated machine pool and proactive approach, not only between departments but with the customer, are the winning factors that lead to the construction of hi-tech complex products.
Thus the company that starts with sheet metal moulding and ends with the design and construction of advanced mechanical-physical complex, finished and assembled products.
From sheet metal moulding to complex product completion, here are two examples for the kitchen robotics sector.
1. Vorwerk Thermomix kitchen robot mixing bowl
The customer is one of the main players in the kitchen robotics sector. With its legendary Thermomix, Vorwerk gained millions of users throughout the world.
Vorwerk has no doubts: in choosing a partner/supplier, the German company focused on raw material quality, maximum attention to details (no imprecision is admitted), problem-solving autonomy and timely deliveries, even with rather high production quantities.
For this reason it chose Minifaber as the manufacturer of its stainless steel mixing bowls (Mixtopf).
A production that occurs on a dedicated line where, starting from deep drawing sheet metal and through a series of other cold processes, the AISI 304 stainless steel mixing bowl that completed the most successful kitchen robot is achieved.
But what are the key aspects in the construction of this complex product?
Surely the operation cycle required in the production of the stainless steel mixing bowl is particularly articulated. It starts with the raw material selection moving on to sheet metal moulding and finishing. The mixing bowl is polished both externally and internally, electrical components are applied by laser welding and plastic parts are assembled through other processes. Functional and control tests are conducted before deliver so that every finished and assembled item can be delivered to the purchaser without any imperfection, ready to be assembled with the rest of the kitchen robot components.
Surely a complex production process that only a few companies in the world are able to achieve.
2. Philips Saeco coffee maker
The rapid response to customers’ production needs along with complex metal product design and construction capacity have led Minifaber to work with another strategic player in the kitchen appliance sector.
Specifically, in the home coffee maker division, Minifaber is Philips Saeco’s partner for the entire Intelia model construction process.
In its second factory, Minifaber produces every metallic component for the Intelia coffee maker: from grills to trays, from filters to the body, as well as the assembly of the various parts and components.
The raw material is AISI 304 and AISI 430 anti-touch stainless steel that is cold rolled, passing through shearing and bending, wrapping and assembly with plastic components. Lastly, the pre-assembled parts are assembled to achieve the finished, ready-to-use product.
The result is a complex, finished and assembled product that Philips Saeco can manufacturer relying on a single supplier: Minifaber.
Do you want to see all of Minifaber's products?