Breadcrumb
Laser cutting and bending: how do they affect each other?
In the sheet metal cold moulding industry, each process affects the next and, to achieve excellent results in terms of quality and precision, each production process phase must be professionally completed. Cutting and bending, specifically, are closely correlated processes which, to result in high performance products, must be carefully performed. This is how Minifaber was able to reduce its margin of error and optimize production schedules.
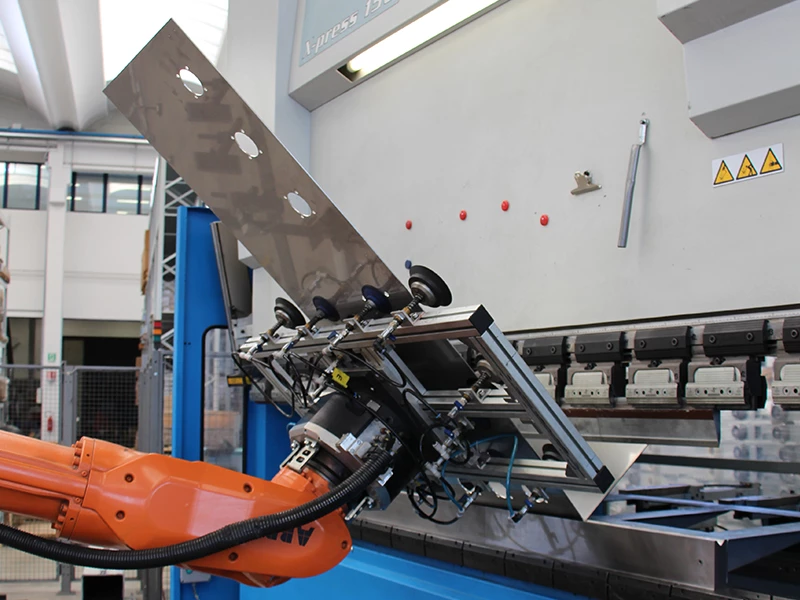
On this page, we will discuss:
- Laser cutting and bending: two consecutive processes
- Process efficiency
- The innovation within laser cutting and bending
- Minifaber reduces the margin of error thanks to robotic systems
Laser cutting and bending: two consecutive processes
Whether we are dealing with hardware components or larger sheet metal parts, these elements need to be cut to the shape defined in the design stage and then bent to obtain the exact piece required by the customer.
Thus, sheet metal cutting and bending are two consecutive processes. In this case, errors during the first or second phase could result in the cancellation of the other, with a significant waste of time and material.
Process efficiency
As we have already pinpointed, laser cutting and bending are two core processes in metalwork.
In fact, thanks to new laser technology, cutting metal sheets is not only more efficient, but provides unequaled accuracy in creating extremely detailed and intricate shapes.
On the other hand, bending is instrumental in shaping components, molding them into the designed form.
These two processes should always be aligned and work synergically. Only in this way, an accurate laser cut can result in a smooth bending, reducing warping and enhancing the finished product quality.
The innovation within laser cutting and bending
Laser cutting and bending have evolved, developing a new approach to metal molding.
More and more companies are opting for robotic systems and computer numerical control (CNC) panels that make these processes automated, increasing productivityand decreasing errors.
Naturally, this technological evolution has heightened the accuracy level required both in laser cutting and bending operations.
As a result, components are:
- more precise
- more reliable
- more efficient
- more consistent
- faster
Automation has changed the face of cold metal work, reducing human intervention, fatigue, and potential human errors, boosting the overall workplace safety.
Minifaber reduces the margin of error thanks to robotic systems
Since the margin of error significantly affects costs and production schedules in coupled processes, Minifaber has introduced robotic systems and numeric control systems in its departments that reduce human intervention and thus avoid component breaks, machine downtime and excessive material scraps during the various processing phases.
This is the case with sheet metal laser cutting and bending systems that are activated by single department workers but fully completed by the machines. This speeds up production, provides more accurate cuts and bends and results in higher quality components.
Read more about our metal laser cutting technologies!
Using automatic laser cutting and bending systems, but also robotic welding machinery, results in the production of components that increasing meet design specifications and tolerances, increasing our production quality and satisfying the need of customers who are more attentive to single part details as well as production schedules and costs.