Breadcrumb
Laser cutting metal: how it works and why choose it for industrial applications
A precision process for custom machining
Laser cutting metal is a high-precision thermal process widely used in industrial processes where minimal tolerances, high repeatability, and edge quality are required.
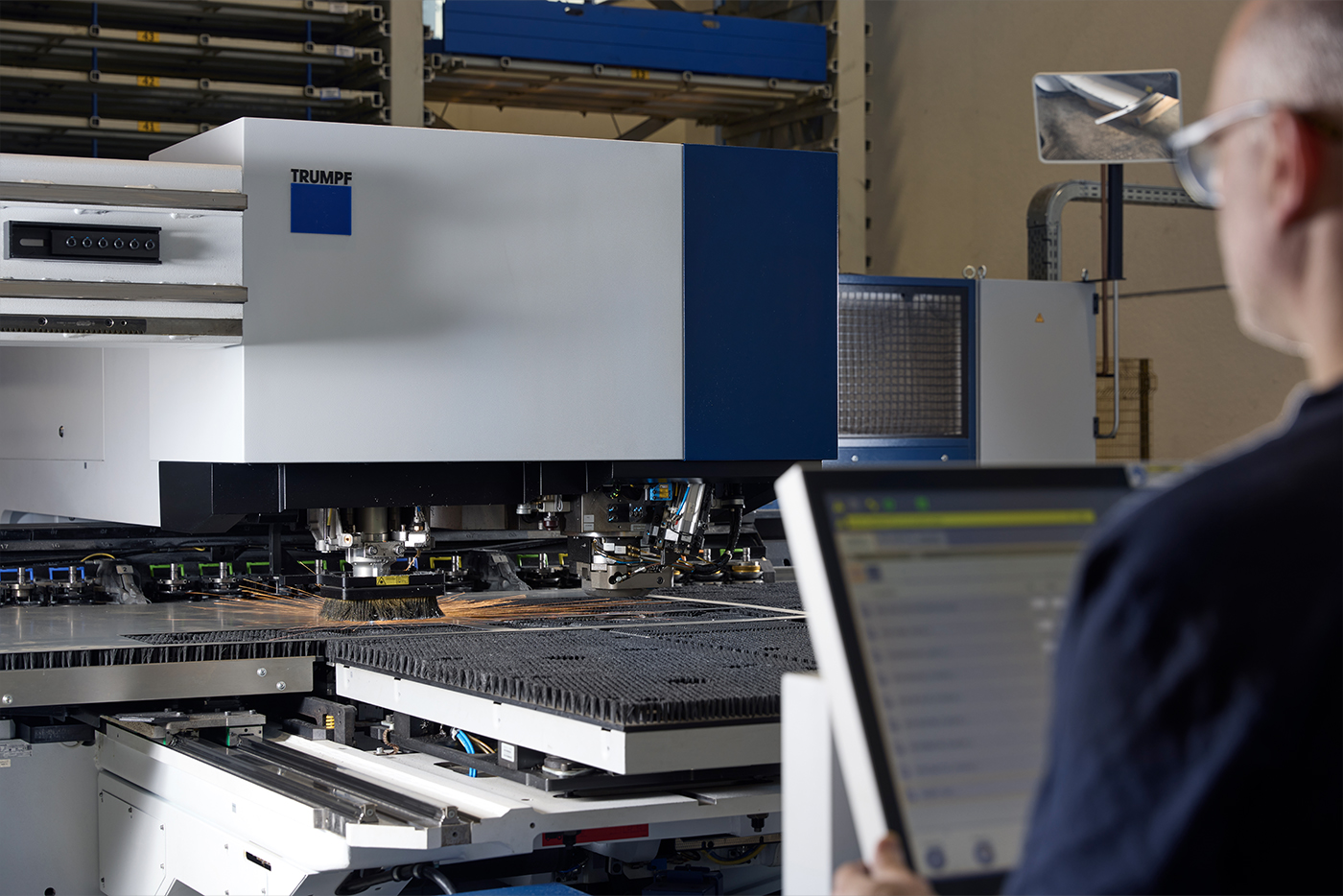
Laser cutting metal is a high-precision thermal process widely used in industrial processes where minimal tolerances, high repeatability, and edge quality are required.
In particular, Minifaber uses CNC technologies with 2D and 3D laser systems capable of working with various metals – from iron to stainless steel to aluminum – guaranteeing optimized results for every type of project.
The principle behind the process is the generation of a laser beam inside a source. The laser beam, which consists of an electromagnetic wave, is conveyed to a lens system through an optical fiber. The lens system that forms the heart of the laser head focuses the laser beam at a point called the focal point, which is located directly on the sheet metal. The effect produced by the laser beam concentrated on the sheet metal is the localized melting of the material, which cuts the sheet metal. An auxiliary gas jet – oxygen or nitrogen – removes the molten material from the cutting groove, leaving clean, sharp edges free of burrs. All this takes place under computerized numerical control (CNC), which allows for maximum automation and repeatability, even on high-volume production runs.
From design to cutting: a continuous flow
The laser cutting metal process begins with a technical co-design phase with the customer until its approval.
The design of the piece is used by CAM software which, through a nesting program, calculates the best layout (in terms of space and orientation) of the pieces to be obtained from a flat sheet of standard-sized sheet metal.
The nesting program is imported onto the cutting machine where the interface with the CNC system allows all cutting parameters to be set in detail: feed speed, laser power, type of assist gas, beam focus, as well as creating the cutting path
Each setting is calibrated according to the type of metal, its thickness, and the desired geometry.
Minifaber processes metals in sizes up to 1250x2500 mm and even great thicknesses, thanks to up-to-date machinery that includes:
punch-laser combination machines, which combine the versatility of the laser with the speed and precision of punching. These are 2D laser systems with, usually, a CO₂ source.
3D laser systems with fiber source, ideal for three-dimensional parts that have already been deep-drawn or molded and for cutting all materials, including copper.
Assist gases: oxygen or nitrogen depending on the process
In laser cutting metal, the assist gas plays a fundamental role as it directly influences the quality of the cut, the speed of execution, and the finish of the piece.
The choice of gas, oxygen or nitrogen, depends on various factors, including the type of metal being processed, the thickness of the sheet metal, the desired aesthetic result, and productivity requirements.
Oxygen is mainly used for cutting carbon steel and ferrous metals. Its function is not only to remove molten material from the cutting point, but also to actively participate in the combustion reaction, generating additional heat. This exothermic reaction makes it possible to increase the feed speed and cut even thicker sheets with reduced energy consumption. However, the use of oxygen causes greater oxidation of the edges and may require subsequent treatments if an aesthetically clean or oxide-free surface is required.
Nitrogen, on the other hand, is the ideal gas for laser cutting stainless steel, non-ferrous alloys, aluminum, brass, and copper. Unlike oxygen, nitrogen does not react chemically with metal during the process: its action is purely mechanical, simply expelling the molten material through pressure.
This prevents the formation of oxides, preserving the surface integrity of the material and ensuring smooth, shiny edges free from discoloration, without the need for post-processing. In addition, nitrogen is essential for applications where a flawless aesthetic finish is required or where contamination by oxygen could compromise the functionality of the component, such as in the food, pharmaceutical, or medical sectors.
Every Minifaber laser system is designed for combined and alternating use of assist gases, allowing for quick modification of process parameters according to the specific requirements of each order.
Thanks to numerical control systems, switching between nitrogen and oxygen is automatic and precise, allowing highly flexible and efficient management even for mixed production or products with heterogeneous technical characteristics. This setup ensures high operational flexibility and quick response to customer requests, while maintaining high-quality standards.
Why choose laser cutting metals?
From a technical point of view, the advantages are clear:
high precision, with dimensional tolerances down to +/- 0.1 mm
no contact between tool and material, eliminating mechanical wear and reducing maintenance
production speed, especially on medium to large batches
edge quality, without the need for further finishing
possibility of performing complex cuts, even on pre-treated materials or with holes of various shapes
compatibility with a wide range of metals, including reflective materials and special alloys
In addition, the process is environmentally friendly: it does not produce chips, does not require the use of lubricating oils that must subsequently be washed off, minimizes waste, consumes less energy than other traditional technologies such as plasma or oxy-fuel cutting, and, finally, requires limited and inexpensive equipment compared to other cutting processes such as shearing.
A service geared towards industrial production
Minifaber offers a comprehensive laser cutting metal service for the production of both finished and semi-finished parts for subsequent processing (bending, welding, surface treatments).
Our facility is organized to respond to both prototyping needs, with rapid response times and validation tests, and batch orders with integrated in-line quality control.
Each project is followed by specialized technicians who work alongside the customer from quotation to delivery, ensuring maximum consistency between technical design, required performance, and final use conditions of the items.
Contact us for more information.
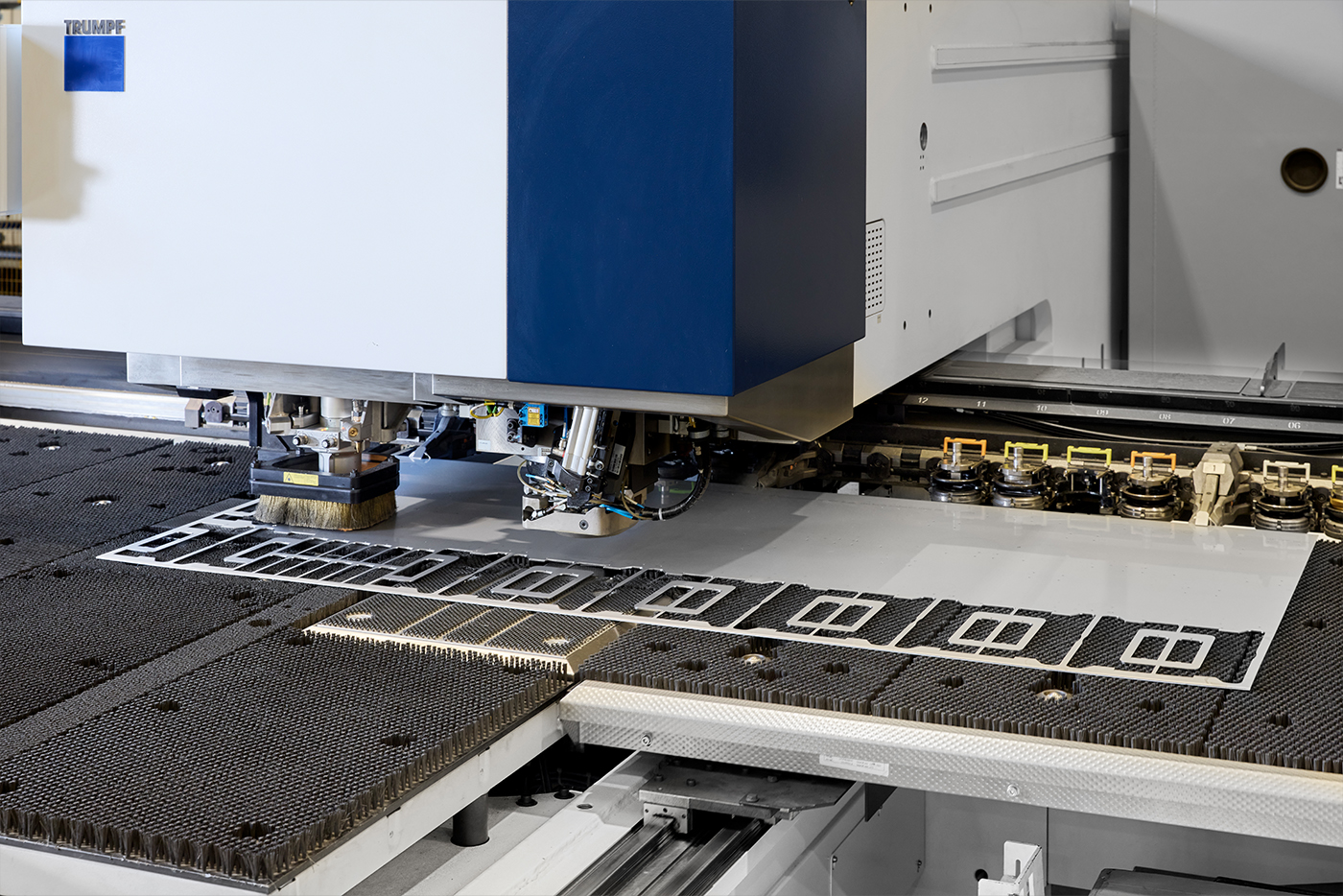