Breadcrumb
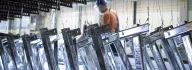
Metal surface treatments
Minifaber uses suppliers who specialize in metal surface treatments and have a strong local presence, resulting in decreased production times and costs, as well as highly professional partnerships.
The purpose of these metal treatments is to give the product an optimal finish that, not only gives it aesthetic value, but also makes it more durable against oxidation and increases other technological properties such as surface hardness, self-lubrication, and other application-dependent requirements requested by customers.
The surface treatments provided by Minifaber through its partners
In detail, Minifaber can provide the surface treatments listed below on aluminum, stainless steel, copper, ferrous materials, and special alloys.
Galvanizing
In general, galvanizing is the process by which a part is coated with zinc (“galvanized”) in order to protect it from corrosion. There are several stages to galvanizing: the galvanic process is the most widely used, as galvanizing involves proper surface preparation through chemical and electrolytic degreasing processes, the actual galvanizing, and subsequent passivation, which makes the galvanic deposit stronger. The treatment can be followed by appropriate dehydrogenation to eliminate any hydrogen embrittlement.
Various types of zinc deposition and possible subsequent sealing are available to further increase oxidation resistance of the galvanized layer. The professionalism and competence of our partners ensure a high-quality supply that meets the specifications required by the customer.
Painting (cataphoresis, powder)
This is a protective treatment, especially for ferrous materials that otherwise naturally tend to oxidize, which can greatly increase the aesthetic performance and long-term corrosion resistance and wear resistance of the base material. There are several processes for applying paint: from cataphoresis to powder coating and even liquid painting.
Anodizing
Anodizing is a surface treatment for aluminum that increases its oxidation resistance by increasing the natural self-protective coating that forms on aluminum. Anodizing can also meet aesthetic requirements as it can be done in a variety of bright colors.
Stainless steel electropolishing
Stainless steel electropolishing consists of removing the most superficial layer from stainless steel (between 10 and 40 microns) in order to make it more corrosion resistant. Electropolishing therefore removes the outermost layer of metal, which may be altered during fabrication and often contains machining oil residues. It offers very good aesthetic appearance and, as mentioned above, a significant increase in corrosion resistance.
Stainless steel pickling and passivation
Minifaber uses these surface treatments to clean and protect its stainless steel products. These are chemical treatments performed by specialized companies.
Nickel plating
A distinction is made between electrolytic nickel plating and chemical nickel plating, the latter being decidedly more precise and adheres better to the part geometry, which is why it is much more widely used. Nickel plating significantly increases surface hardness and thus increases durability against corrosion and wear, improves aesthetics and hygiene, making it versatile on various materials.
Chrome plating
This is a surface treatment in which a layer of chromium is applied to a metal part to improve its appearance, strength, and functionality. It is particularly valued for its brightness and hardness, as well as its ability to protect the base metal. There are two types of chrome plating, decorative plating, which is used for aesthetic purposes, and hard (thick) plating, which is used to increase the hardness, wear resistance, and durability of the part.
Chromate treatment
This is a chemical surface treatment that does not involve deposition but converting the base material surface, replacing it with chromium compounds. The treatment makes it oxidation resistant, promotes adhesion of paints, and facilitates self-construction of the protective layer in the event of micro-damage.
Silver plating
Silver plating is done by an electrolytic process and is based on the same principles as galvanizing or chrome plating. This process achieves an excellent result because of the conductive and protective capacity of silver. In addition, it can also be masked, and selective silver plating can be performed on particular areas of interest on a part. It is valued on parts for the electromechanical industry to improve electrical conductivity and in the medical industry for its antibacterial properties.
Phosphating
Phosphating is a chemical surface treatment applied to metals, mainly steel, zinc and aluminum, to form a layer of insoluble phosphates on the material surface. This protective layer improves corrosion resistance, and promotes adhesion of coatings such as paints or lubricants.
Polishing
This is a metal surface finishing treatment that gives a final polished and smooth effect. This usually starts with an initial stage in which the part is preprocessed by deep cleaning (grinding or passing an abrasive paste) followed by the actual polishing. It is particularly used on stainless steels to improve appearance and corrosion resistance.
Shot peening
Shot peening is used to increase fatigue resistance and improve the surface appearance of metal components, especially stainless steel. As the word suggests, shot peening is done by a blasting the parts with cold spherical steel or glass shot. The kinetic energy generated by the impact causes plastic deformation on the metal surface, which helps to eliminate residual stresses and hence improve the aforementioned fatigue resistance of metal components.
Sandblasting
This is similar in some ways to shot peening, but with completely different functions. In sandblasting, as with shot peening, the most superficial part of the metal object is blasted, but in this case by a jet of sand and air with larger grains. This serves to completely remove a particularly damaged/corroded area of a metal surface. Sandblasting is also used to improve the aesthetic appearance of welded structures.
Vibratory finishing
This is a mechanical surface finishing process used to remove sharp edges, shearing burrs and oxides from metal parts, and to improve their aesthetic and functional quality. The process is performed by controlled vibratory movement of parts immersed in a container together with an abrasive material, specific liquids, and in some cases chemical additives.
Minifaber, professional metal surface treatment services for small and large quantities
Contact us without obligation for more information
Minifaber, 65 years of cold metalworking know-how for small and large quantities.
Contact us for a quote and feasibility study
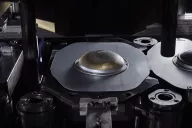
COMPLETED PROJECTS
Flame diffuser for boilers
In research and development, the client designed a new type of boiler inside which the burner is mounted. This part is the heart of the operation and performance of the entire system. The flame spread must meet certain requirements, otherwise the whole system may not function properly.
The main challenge was to molding the upper part with more than 5,000 holes of extremely small diameter.