Breadcrumb
Metalworking
Minifaber works iron, stainless steel, copper, brass in both large and small quantities.
We perform cold metalworking on large and small quantities of metals, from designing and constructing molds and welding and assembly equipment, to laser cutting and punching processes. Our established expertise means we are able to meet customers’ needs to perform the metalworking most in demand.
The entire production process is in-house: our in-house personnel handles every single stage of the fabrication process, from initial design, through sampling, to mass production of parts.
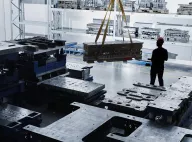
Different metalworking types
Minifaber has the expertise and technologies needed to perform various processes on metals, including complex ones.
Click the tabs below to explore the many metal fabrication techniques Minifaber performs.
Cold metalworking
Minifaber specializes in cold metalworking, processes that deform the material at ambient temperature. This deforms the metal with high precisions standards while controlling its properties and ensuring its integrity.
This is a particularly valued production process for making components with tight tolerances and complex fabrication techniques, where it is essential to preserve the metal structure.
Moreover, cold metalworking offers the great advantage of making complex shapes on thin materials, offering a significant reduction in production costs.
Minifaber, professional cold sheet metal fabrication services
Contact us without obligation for more information
Every metalworking process has its own application sector
Expertise, passion and continuous technical advances allow us to work with the best companies in key application fields:
- ELECTROMECHANICAL
- FOOD PROCESSORS
- VENDING
- MEDICAL
- GAS DISTRIBUTION
- HOME/PROFESSIONAL APPLIANCES
- ENERGY DISTRIBUTORS
- PROFESSIONAL LIGHTING.
Minifaber, 65 years of cold metalworking know-how for small and large quantities.
Contact us for a quote and feasibility study
Choose Minifaber to make your dies
With over 65 years of experience in the industry, we are able to support you in the design stage of the semi-finished or finished products, and complete the production with consistently excellent results. The entire process, from die design to finished product logistics, takes place in-house, following strict quality controls and with highly trained, specialized personnel.
We are ready to work with you. Contact us to talk to one of our technicians.