Breadcrumb
Sheet metal cutting: how it is done and how it works
Sheet metal cutting is a cold mechanical process, particularly suitable for large production quantities. Used to obtain both semi-finished and finished products, blanking depends on the combined action of a die and a punch that penetrates the sheet: this is how it happens in Minifaber and the services we offer.
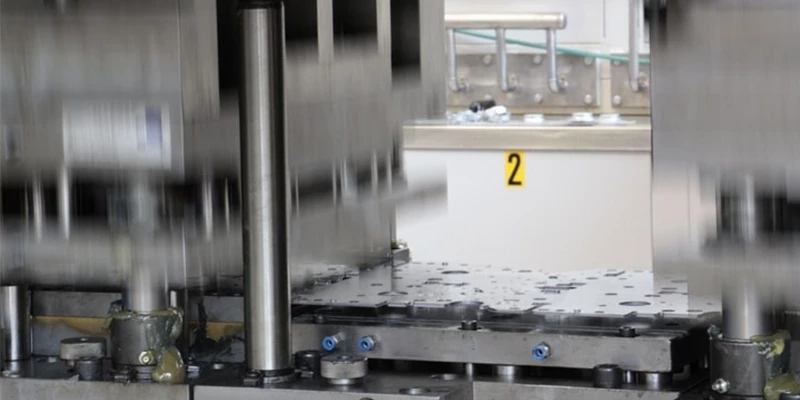
Sheet metal cutting aims to create finished or semi-finished products with precise edges. To limit the inevitable blanking burr, in Minifaber we are careful to use only adequate presses with non-slip sliding on the guides, carefully machined dies that always guarantee the best results of the various operations.
To learn more, read this article:
- Minifaber blanking services
- High-performance dies for sheet metal cutting and blanking
- Industries we work for
- How sheet metal cutting takes place
Sheet metal cutting with Minifaber
Minifaber offers a state-of-the-art sheet metal cutting service thanks to the experience accumulated over years of activity and to the fleet of machines, consisting of 17 mechanical presses and 2 cleaning systems in line with them.
We perform blanking on sheets made of:
- ferrous materials
- stainless steel
- aluminum and its alloys
- copper and its alloys such as brass
- special alloys such as cupronickel
How to make a high-performance die for sheet metal cutting and blanking
When designing the blanking dies, we accurately calculate the clearance between the die and the punch. This takes into account the thickness of the sheet, the type of material to be cut, the speed of the press and lubrication.
The material to make punches and dies must be chosen carefully according to the same criteria listed above. The steel mills are chosen among the best on the world market.
The mechanical processing of the active parts of the die is carried out accurately with high-performance machinery such as a 5-axis milling machine and electro-erosion with multiple trims.
All die parts are dimensioned to ensure maximum rigidity and precision.
Industries we work for
In this way the pieces are ready to be used in a variety of sectors:
- electro-mechanic
- medical
- robotics
- lighting fixtures
- home appliances
- vending
- gas distribution
How does sheet metal cutting and blanking work?
Only in-depth knowledge and experience can determine the clearance, shapes and dimensions of the punch and die. In fact, they must be able to move smoothly and precisely, respecting the construction criteria of the die and depending on the material to be blanked and the requirements of the customer's drawing.
The result is a flawless blanked sheet, while the machinery used is protected from premature wear.
The defects of an imperfectly calibrated blanking
If, during blanking, the clearance between the die and the punch is too high, the excessive space between the two elements causes the sheet metal edges to bend, round them and produce abundant burrs.
If, on the other hand, it is too low, the space between the two parts is reduced, the contact between the die and the punch causes rapid wear of the same and of the die in general, and the semi-finished or finished pieces have equally high burr due to drawing the sheet metal.
A very useful function is performed by the blank holder which avoids the lifting and bending of the sheet metal during blanking, while during the extraction of the punch which takes place in the return stroke of the press, it prevents the sheet from clinging to the punch and raised together with it.
Finally, for the blanking to work properly, the punch must be guided with precision by suitably machined plates:
- the die itself must have an effective guiding system made from precision columns and bushings
- the movement of the press slide must have no slips and the guides must be periodically adjusted
- lubrication plays a fundamental role in avoiding seizure and sticking of the sheet metal on the active parts of the die
State-of-the-art blanking
How to be sure, then, to obtain state-of-the-art blanking? It is necessary to check that the cut edge does not have chips, that there is a small radius on the side where the punch enters and a small burr on the exit side of the punch.
Between the two sides on the thickness will be a blanked part and a torn part which are typical of blanking.
With all these precautions you will achieve:
- a state-of-the-art blanked piece
- minimum burrs
- precision of the blanked pieces
- lack of deformations on the blanked piece
- longer die life
- longer press life and efficiency.