Breadcrumb
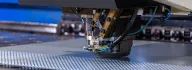
The aluminum punching process in Minifaber
Aluminum is a lightweight material, and features high stiffness. It has good electrical conductivity and thermal conductivity. For these reasons it is used in multiple industries.
Aluminum punching is done by means of special machines called punch presses. These machines and the tools they come with can cut holes and openings of any geometry on sheet metal of standard or custom formats. This results in semi-finished and products made to drawing directly from the original sheet. Punching also gives rise to other fabrication techniques such as small bends, stamping, threading and edge banding.
Aluminum has lower mechanical strength than ferrous materials and stainless steel. Therefore, a proper tool set consisting of a die, punch and blank holder should be identified. The clearance between punch and die must be carefully chosen to avoid forming a lot of burrs or deforming the sheet metal.
At Minifaber, punch presses are combined with laser cutting. The machines are therefore equipped with both a punching head and a laser cutting head. This exploits the benefits of the two technologies to improve productivity and product quality.
In order to better exploit and optimize the sheet metal from which the parts are made, our qualified and specialized personnel create a nesting CAD design. This provides a quality cutting process that reduces material costs and turnaround times.
Minifaber, professional aluminum punching services for small and large quantities
Contact us without obligation for more information
Metal punching
Minifaber's metal punching offers precise, custom solutions that adapt to different materials such as steel, aluminum and others.
Click on the links below to explore the different types of punching offered by Minifaber.